Troubleshooting Second Layer Printing Issues on Mega i3

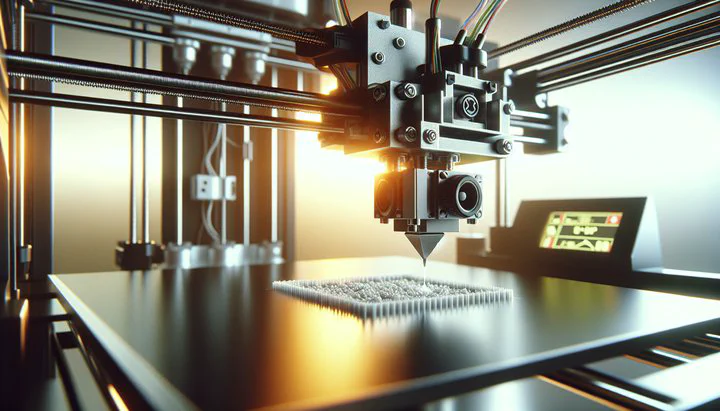
Understanding the Mega i3 Second Layer Issue
If you’re using the Mega i3 3D printer, you might have faced a problem where the second layer of your print just doesn’t seem to work right. This is known as the Mega i3 second layer printing issue, and it’s a common headache for many users. Noticing that the second layer isn’t sticking properly or seems uneven? Don’t worry, you’re not alone! Many makers and engineers encounter this problem, and it can be super frustrating when you’ve prepared everything else perfectly.
But what exactly is happening with the second layer? The second layer is important because it sits on top of the first layer. If the first layer isn’t right, the second can have problems too. Symptoms of second layer issues include gaps, uneven textures, or even complete detachment from the first layer. You might find yourself asking, “Does the first layer affect this much?” Yes, it does!
The Mega i3 second layer printing issue happens often because of several factors. It could be related to printer settings, filament quality, or even how the first layer is printed. Users report that with several models, and the same thing always happens. Recognizing these symptoms early can save you a lot of time and material. As we explore this problem, we’ll also look at why it seems so prevalent among Mega i3 users, ensuring you have the tools and knowledge to overcome it.
Initial Troubleshooting Steps
When you run into the Mega i3 second layer printing issue, the first thing to do is not panic. Let’s walk through some initial troubleshooting steps to get you back on track. These are simple checks you can do to identify and fix the problem.
First, examine your printer settings. Make sure everything is set up correctly. Start by checking the bed level. If your bed isn’t level, the first layer might not adhere properly, causing problems with the second layer. Make sure your printer’s bed is flat. Use tools that come with your printer to check.
Next, ensure that the first layer is printed correctly. You might wonder, “Does the first layer matter that much?” Yes, it really does! If the first layer isn’t perfect, the second layer can’t stick well. Look for signs of uneven lines or gaps. If you notice these issues, you may need to adjust your layer height or print speed.
Don’t forget about the filament quality! Old or low-quality filament can lead to printing problems. Check your filament for moisture or dust. These can affect how well the layers stick together. If your filament is questionable, try using a fresh spool to see if that solves the issue.
Lastly, review the printer’s nozzle temperature and speed settings. Sometimes, a little tweak can make a big difference. Too hot or too fast can cause the second layer to be messy. It’s all about finding that sweet spot where everything works together smoothly.
By following these steps, you’re setting a strong foundation for solving the Mega i3 second layer printing issue. If these checks don’t fix it, don’t worry! We’ll explore more advanced solutions next. But for now, get these basics right, and you’ll be more confident when you send it to print again.
Advanced Solutions and Techniques
If you’ve tried the basics and you’re still seeing the Mega i3 second layer printing issue, it’s time to dive into more advanced troubleshooting. These techniques will help you fine-tune your printer and get those layers sticking perfectly.
Adjusting the Z-Offset is a great place to start. The Z-offset determines how high the nozzle is from the print bed. If it’s too high or too low, the layers won’t bond properly. You can adjust this setting through your printer’s menu or software. Start by making small changes and test-printing to see if it improves your results.
Next, let’s talk about slicer settings. The slicer is a program that tells your printer how to make your model. Sometimes, tweaking these settings can solve persistent second layer issues. For instance, adjusting the layer height or print speed can help. Also, consider changing the infill pattern or density. These tweaks can make a big difference in how the second layer adheres.
Another advanced step is to update or modify your firmware. Firmware is the software that controls your printer’s hardware. An outdated version might cause printing issues. Check if there’s a new update available for your Mega i3. Some users even modify their firmware settings to improve layer adhesion. This requires some know-how, but it can be worth the effort.
Finally, if you’re using a Mega i3 for €20 or have a budget-friendly model, these advanced techniques are even more vital. Cheaper printers might need extra calibration to perform well. Keep experimenting with these methods, and remember, patience is key.
By implementing these advanced solutions, you’ll be well on your way to resolving the Mega i3 second layer printing issue. Whether it’s adjusting the Z-offset or tweaking slicer settings, these techniques will help you print with confidence. Keep refining your approach, and soon you’ll be able to send it to print without worrying about that pesky second layer!
User Experiences and Common Patterns
When dealing with the Mega i3 second layer printing issue, hearing from others who have faced the same problem can be very helpful. Many users have shared their experiences, and we can learn a lot from their stories. By understanding common patterns in these experiences, you can better tackle the problem yourself.
One common thing many users report is that they’ve tried several models, and the same thing always happens: the second layer doesn’t stick, or it looks messy. This pattern suggests that the issue might not just be with one specific print or even one specific setup, but rather something more general that affects many Mega i3 printers. For example, some users found that the problem often arises due to slight misalignments in the printer’s build plate or inconsistencies in filament quality.
Another pattern observed is related to the first layer. If the first layer isn’t perfect, the second layer won’t stick well. This highlights the importance of getting that first layer just right. Community feedback often emphasizes the need for proper bed leveling and the right settings for your specific filament type. If the first layer is solid, it provides a stable foundation for the rest of the print.
Feedback from the community also points to how various environmental factors can influence printing success. For instance, some users noted that the room temperature and humidity can affect how well layers adhere to each other. Keeping your printing area stable and controlled can help mitigate these issues.
Finally, many users stress the importance of regular maintenance and adjustments. Over time, even small shifts in your printer’s components can lead to recurring problems. Regularly checking and recalibrating your printer can prevent these pesky second layer issues from cropping up.
By learning from these user experiences and recognizing these common patterns, you can better understand the Mega i3 second layer printing issue. With these insights, you can make informed adjustments to your setup and increase your chances of smooth, successful prints. Remember, every printer and setup is unique, so keep experimenting until you find what works best for you.
Preventive Measures and Best Practices
Preventing the Mega i3 second layer printing issue can save you a lot of time and hassle. With a few best practices, you can minimize problems and enjoy smoother printing experiences. Let’s explore some preventive measures to help you print with confidence.
First and foremost, focus on regular maintenance. Keeping your Mega i3 printer clean and well-maintained is crucial. Make it a habit to check the printer’s components regularly. Ensure that the build plate is clean and free from any residue. Dust and leftover filament can cause layers not to stick properly. Also, inspect the nozzle for clogs or buildup, as these can affect print quality.
Next, pay attention to optimal settings. Every filament type has its own ideal temperature and speed settings. Before you send it to print, make sure your printer is calibrated to suit the filament you’re using. Start by adjusting the temperature settings for the hot end and the bed. Many users find that a slightly higher bed temperature can improve adhesion for the first few layers, including the critical second layer.
Using quality materials is another important factor. Investing in good filament can significantly reduce printing issues. Poor quality filament can have uneven thickness or impurities, leading to problems like poor layer adhesion. Store your filament properly to keep it dry and dust-free. Moisture can cause filament to swell, affecting how well it prints.
Make a checklist of things to check before you print. This can help catch problems early. This checklist can include steps like checking the bed level, ensuring the filament is loaded correctly, and verifying that the slicer settings are correct for your model.
Finally, stay connected with the community. Engage with other Mega i3 users online to share tips and solutions. This way, you can learn from others’ experiences and discover new ways to improve your setup. Websites like MakerTechGuides are great places to find resources and connect with fellow makers.
By following these preventive measures and best practices, you’ll be better prepared to avoid the Mega i3 second layer printing issue. With a little care and preparation, you can tackle challenges and enjoy more successful 3D printing projects. Keep refining your process, and soon you’ll be able to send it to print with ease and confidence!